Interview with
Laura del Hoyo
R&D Leader at Walter Pack
“Our greatest challenge is integrating sustainability into any innovative process we undertake.”
For several years now, sustainability has become an unwavering goal for Walter Pack and a ubiquitous challenge for its R&D department. The new head, Laura del Hoyo, is aware of the complexity of balancing this goal with the research of new materials and processes in the demanding automotive world. However, she insists on the need to explore new technologies to achieve it: “We must continue working to achieve aesthetics similar to those obtained with virgin materials using recycled materials.”
Q.
A.
Artificial Intelligence, sustainability, Industry 5.0… We are in a moment loaded with challenges for your department. What would you say are the main challenges for Walter Pack’s R&D?
The main challenge, almost a necessity, is to work towards the sustainability of our products and our business. In recent years, sustainability has become integrated into the automotive sector, one of our main areas of business, to the extent that everything must have a sustainable component. For example, if we consider integrating Artificial Intelligence into our processes or products, we must do so in conjunction with that factor. Our greatest challenge is to integrate sustainability into any innovative process we undertake.
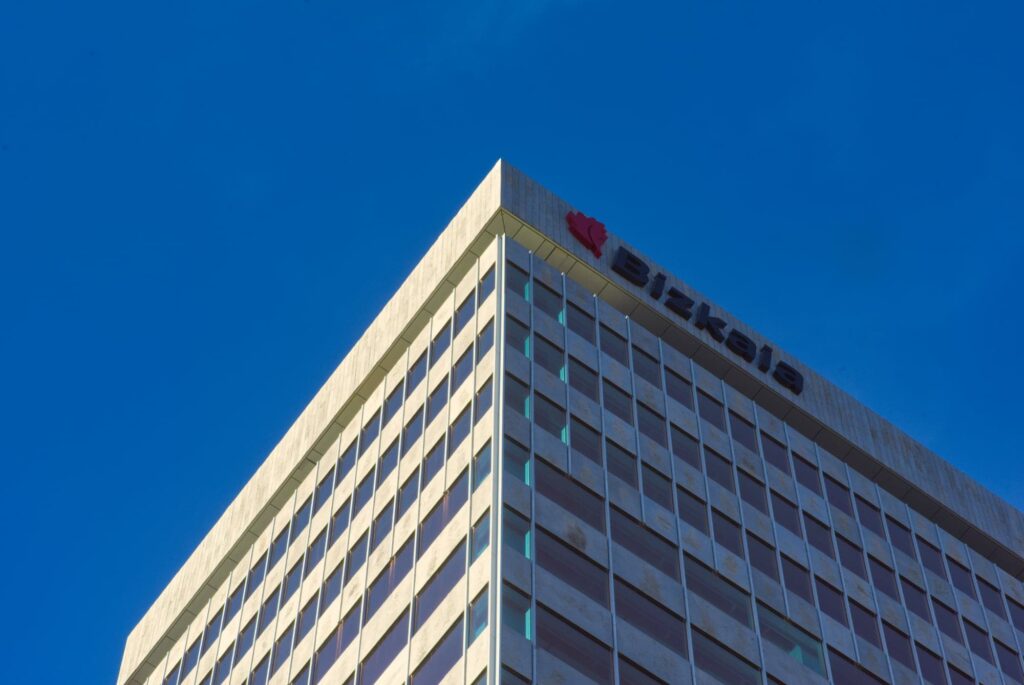
Q.
A.
You recently participated in BAT in an event on innovation in the industrial value chain with EI Manufacturing. Has the use of sustainable materials in the industrial sector shifted from being an option to becoming an obligation?
Indeed, sustainability is no longer optional but a necessary element in the industrial value chain. While all players in the sector have considered it for some time, regulatory regulations implemented over the last three or four years have encouraged us to focus on it in terms of innovation.
Q.
A.
What do major automotive and home appliance manufacturers demand from their suppliers regarding sustainability?
Customers want suppliers and ODMs to incorporate recycled components into their products and the components we manufacture through a dual approach: either they ask us to use a specific percentage of recycled materials in their production, or to use parts with accredited sustainable value, for example, demonstrating that they come from the circular economy.
“Our clients ask us to incorporate recycled materials into the parts or demonstrate that they come from the circular economy.”
Q.
A.
In the current global market, what is the value proposition that allows Walter Pack to maintain its competitiveness?
On the one hand, we need to leverage Walter Pack’s traditionally proven strengths as a manufacturer of decorated and functional films, and on the other, strengthen our commitment to sustainability-related innovation. This means combining our technological strength with a sustainable contribution. We are already experts in this technology, in the production of high-value decorative plastics that integrate functionality. Now, we will add sustainability to our products and offer this option to our customers to provide high added value to the components of their vehicles.
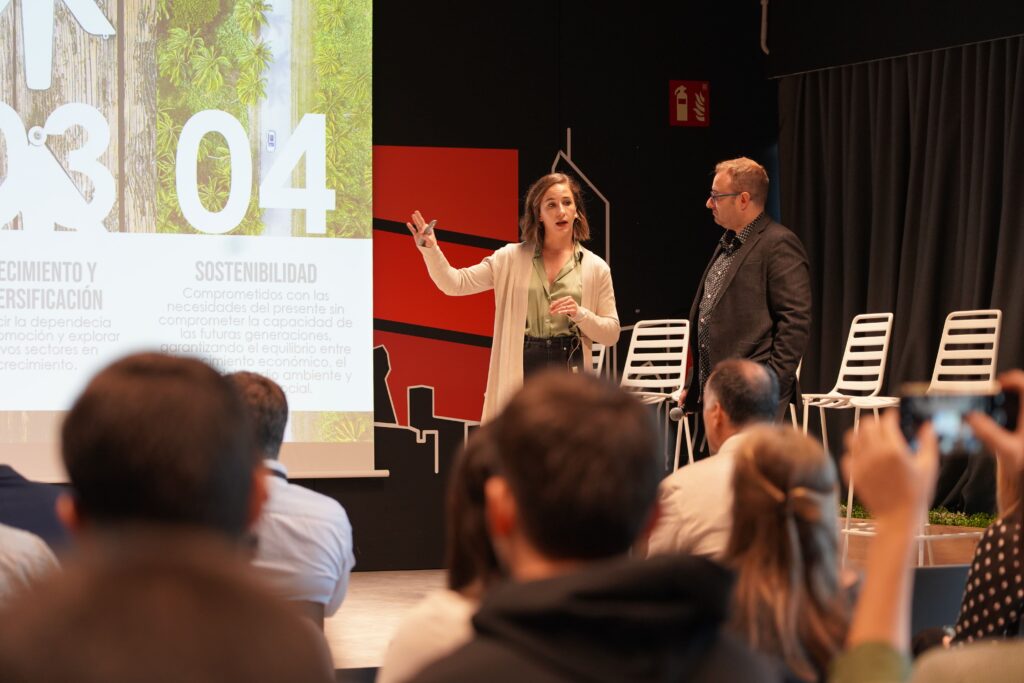
Q.
A.
Q.
A.
Walter Pack presented a project at the EI Manufacturing event with Birziplastik and Gaiker on circular economy applied to materials. What does it consist of, and what role does each party play?
The project is part of Walter Pack’s commitment to deepen the circularity of processes and materials. Its goal is to recover our main waste, the surplus that is not part of the decorative component and was previously discarded, to give it a second life. We want to integrate it into the type of final product we produce. Birziplastik handles the first link in the chain, performing the treatment to convert that waste into a size suitable for Gaiker to process. The technological center then transforms the material to give it the properties needed for reuse as injection material, adding the necessary additives for the mechanical properties required by automotive products. From that point on, we can process the product to produce fully functional plastic parts.
What phase is the project currently in?
At the moment, we are conducting the necessary laboratory tests to replicate the living conditions of this piece inside a vehicle. In parallel, we have started working with other types of cuttings to do the same with other materials.
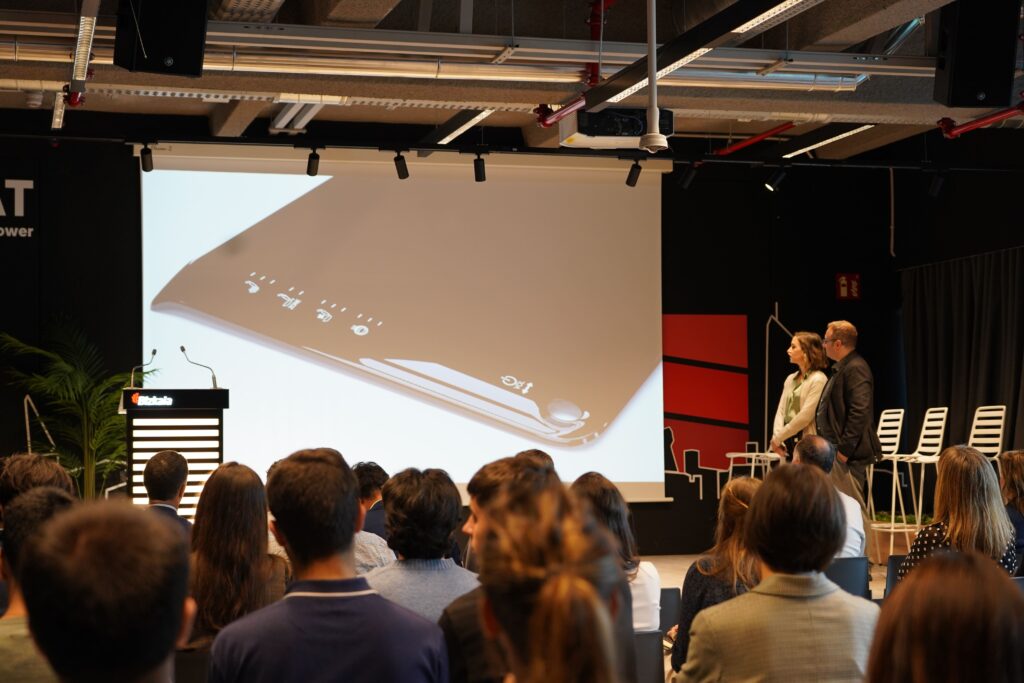
“We presented a project at BAT with the aim of reusing and integrating our waste into the final product”
Q.
A.
Q.
A.
What timelines have been set?
This project is of an R&D nature and concludes as such in 2024. After that, we would have to move to a development phase to, if applicable, achieve approval and offer it.
When it concludes, what added value could it bring to Walter Pack?
On the one hand, it would allow us to offer our customers a product from the circular economy in which our waste would act as substrate material, where applicable. On the other hand, it would give us an economic competitive advantage because we wouldn’t need to acquire virgin material as raw material, and we could offer more economical solutions composed of our own waste. Additionally, using this discarded material would allow us to save on the current waste management in environmental terms.
“This project would allow us to offer more economical solutions composed of our own waste and save on waste management."”
Q.
A.
Is this the only project your R&D department is currently involved in in this field?
Sustainability is one of Walter Pack’s strategic lines, and within it, we are working on several projects simultaneously. One aims to incorporate other waste found in other sectors, such as bottle caps, into our manufacturing processes to become part of the decoration of our pieces. We are also involved in the European Treasure project, which focuses on the disassembly and subsequent recycling or reuse of the elements that make up plastronics components in the automotive sector.
Q.
A.
Q.
A.
What do events like the one organized by EI Manufacturing mean for Walter Pack and the industry as a whole?
Such events represent a great opportunity for companies involved in innovation, like Walter Pack, as they help us refresh our own ideas and serve as inspiration to consider alternative avenues of work. These forums allow us to hear the experiences of other companies from different sectors and update concepts and ideas that we may have preconceived.
In this complex world of plastics, will we ever reach zero waste?
Residues are generated in all industrial processes. The important thing is to work on circularity and try to reintegrate into your processes and products the waste you have generated previously. If we can make the most of our waste, we will reduce the consumption of raw materials and natural resources, leading to greater efficiency and sustainability.
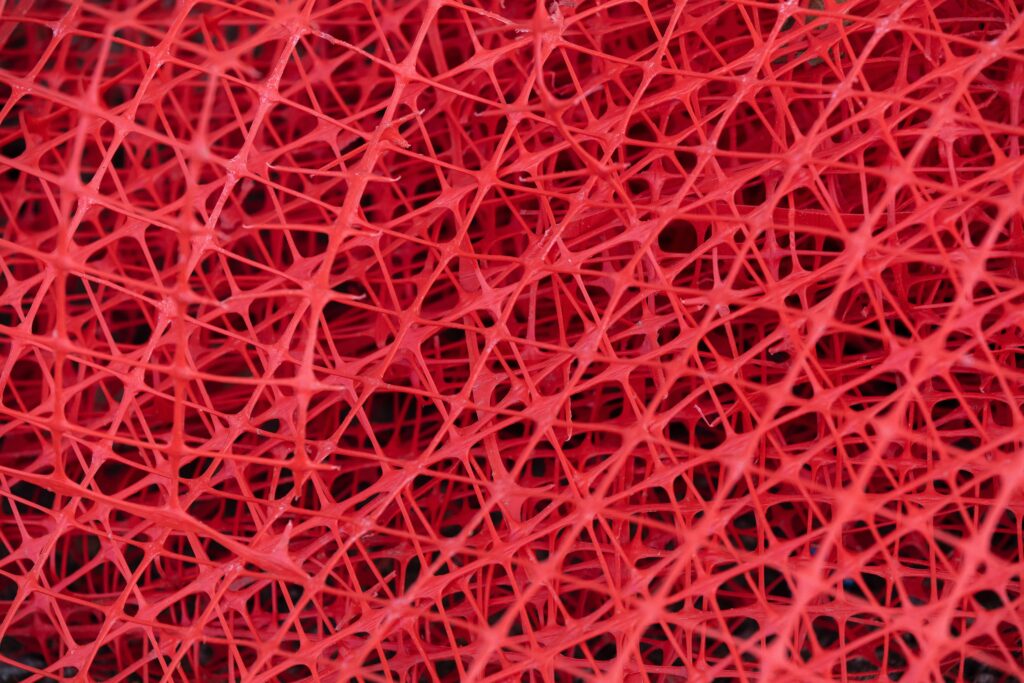
“Events like EI Manufacturing inspire us to refresh our ideas and consider alternative avenues of work.”
Q.
A.
Q.
A.
In this complex world of plastics, will we ever reach zero waste?
Residues are generated in all industrial processes. The important thing is to work on circularity and try to reintegrate into your processes and products the waste you have generated previously. If we can make the most of our waste, we will reduce the consumption of raw materials and natural resources, leading to greater efficiency and sustainability.
Your department not only works for sustainability but also has to address customer demands for new materials, colors, textures, haptic qualities… Is it possible to reconcile both lines of work?
Yes, but it has become one of our main challenges. The automotive industry has very high requirements and demands both aesthetically and functionally. When working with recycled materials, the result is not the same as when using virgin materials. So far, our sector has not been able to achieve the pure and clean aesthetics results obtained with new materials, and that poses a challenge for our department. We must continue working to achieve aesthetics similar to those obtained with virgin materials using recycled materials, explore new technologies to stay relevant, and find new ways of doing things. But I also believe that customers must adapt their demands in some cases: they have to review the demands they have incorporated over the years and see if they are truly necessary from a decorative perspective. What weighs more, perfect aesthetics or manufacturing vehicles with increasingly sustainable materials?